Project Name: SE High School
Building Type: School Building
Location: Canada
Area: 456,000 SF
Inputs: 2D Pdfs, CADs, Markups for (MEPF)
Deliverable: Architecture, Structure, Mechanical, Electrical, Plumbing and Fire.
OVERVIEW
The client was well- established MEP Design consultant. So, they want first LOD 300 model for drawings and then they gave us task to create more detailed model at LOD 400 with coordination and shop drawing creation.
HVAC, water services, drainage, vent, gas services, lighting, power, fire alarm, electrical services, etc. were all included in the internal MEP system modelling. The technical submittals for the extraction of COBIE data were followed in the creation of Revit Families. Along with the 3D Revit Model, we also delivered schedules that included ducts, pipes, cable trays, lights for ceilings, fittings, etc.
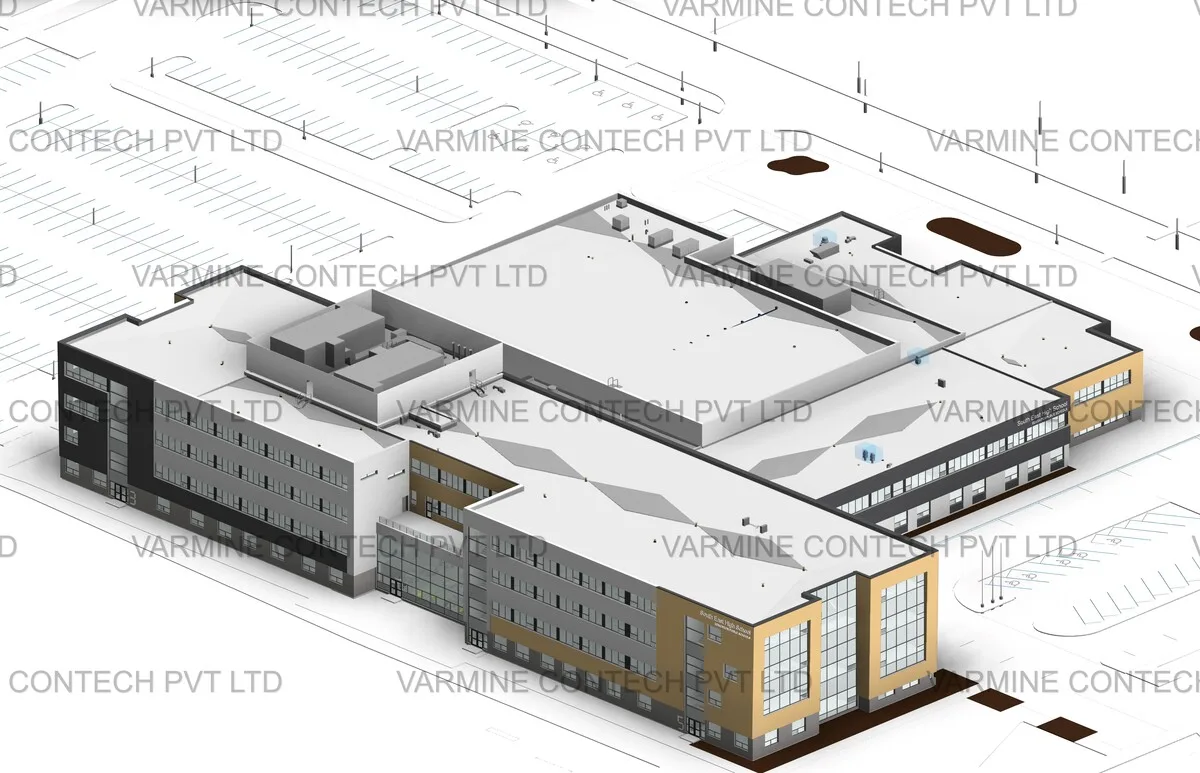
CHALLENGES & SOLUTION
Major conflicts exist in the model between the steel structure (joists) and the duct. The client asked us to coordinate all the services above the ceiling and to pass all the round ducts from the joist gap.
The task was to remove clashes from the ceiling’s smallest possible area. As seen in the pictures below, all mechanical lines are in conflict with the ductwork.
Due to some conduit and round duct conflicts, we coordinated the entire system in accordance with our knowledge and the client’s instructions. In some cases, we create RFIs because not all services fit within a single ceiling. To pass all the services through those areas, we need to change the duct design and reroute other services.
Maintaining the riser alignment in the shaft room was the most tedious task. However, VARMINE was able to successfully complete each task in accordance with the demands of the client.
CONCLUSION
Change orders are a major cause of project cost increases and delays. In this Project BIM Models assist us in detecting the need for any change orders during the design stage, as well as modifications made virtually in the model rather than physically in the construction. Updating a virtual model is less expensive than disassembling and reassembling actual installations, resulting in lower material and labor costs.
It makes it simple to detect location conflicts between multiple MEP components. If two building systems overlap, the corresponding team is notified. When equipment location conflicts reach the construction phase, they can lead to change orders and project delays. BIM reduces the likelihood of errors and problems on the job site.